Sapphire grinding and polishing
- 发布时间:2022-05-13
- 访问量:810
- 访问量:810
- 发布时间:2022-05-13
- 访问量:0
The process of grinding and polishing sapphire substrate
1. Waxing
The primary action of the LED chip grinding process is "waxing", which has the same meaning as the CMP chemical grinding of silicon chips. Fix the chip on the iron (Lapping process) or ceramic (Grounding process) disc. First apply solid wax evenly on the disc heated at about 90~110°C, and then place the front of the chip and attach it to the disc. After pressurizing and cooling, the chip is indeed fixed on the disc surface, completing the waxing action. .
2. Grinding
After the waxing process is completed, the next process is the "grinding process" with the highest destructive power.
In the past, the most mature grinding process was Lapping, which is to use alumina grinding powder for the first grinding of the chip. Its operation method is to use a dial indicator to measure and set the diamond point on the periphery of the iron plate, and then place it on the grinding plate and use grinding powder for grinding. The purpose of using the diamond point is to grind the chip to the set thickness, because the hardness of the diamond is the highest, so the chip will not be worn again.
However, since the blue LED substrate is sapphire and has high hardness, the process time will be too long when lapping is used. Therefore, in recent years, the chip grinding of blue LEDs has been carried out by means of Grinding, which reduces the processing time.
Grinding process equipment can be divided into two types: horizontal and vertical. The horizontal grinding machine refers to the grinding motor parallel to the horizontal plane, which can be applied to the grinding design of less than eight pieces. However, in the case of 12-piece grinding, this design method cannot be used because the ceramic disc is too large. Vertical grinder means that the grinding motor is perpendicular to the horizontal plane, and the design of grinders with more than eight pieces is mainly based on this design.
In the Grinding process, a diamond grinding wheel is used with coolant (cooling oil + RO water or DI water) or diamond cutting fluid to grind chips. Although the cooling method will vary according to the process concept and experience of the original designer, it does not affect the results of the process. In this process, the most important thing is that the adjustment of the working axis and the grinding wheel axis must be parallel. Then there is the grindstone structure of the grinding wheel.
Due to the high speed and efficiency of the Grinding grinding process, if the chip thickness can be reduced as much as possible during grinding, the man-hour and cost of polishing can be reduced. However, grinding is a highly destructive process, so chip thinning has a limit value; in addition, the scratches caused by diamonds in the grinding process are about 15um, so the finished thickness value also affects the thickness setting of grinding thinning .
However, in the used Grinding grinders, whether it is T brand, W brand, SF brand, etc., the maximum limit is 95~105um. Due to the hardness and warpage of the sapphire substrate, the results below 100um after completion are quite unstable.
Therefore, the LED grinding process is mainly based on the combination of equipment design and user experience. However, the nature of the chip is still the main factor affecting the results.
3. Polishing
After the chip is ground, the next process operation is "polishing". The purpose is to deal with deep holes after Lapping grinding, or deep scratches after Grinding grinding. Generally speaking, the depth of holes after lapping is about 10um, and the depth of scratches after grinding is 15um~20um.
As far as the polishing process after Lapping is concerned, most of the polishing discs use polyurethane pads, which is generally called soft polishing. Soft polishing can make the surface bright as a mirror after the process operation, but its cutting rate is extremely low, about 0.2 um/min. Another polishing method is to use tin and lead disks. Because the disk surface is made of metal, it is generally called hard polishing. The cutting rate of hard polishing can reach 0.7~1 um/min, and the processing speed is faster than that of soft polishing. However, polishing with metal discs carries a higher risk. Although tin and lead are soft metals, the condition of the disk surface must be monitored very carefully, especially the trimming of the disk surface. If there are metal particles that are not removed after trimming, they will be fragile after polishing.
Therefore, in order to increase the cutting rate and the stability of the disc surface, in recent years, there has been a new type of polishing disc, the disc surface is resin, and the base is copper. It is now called "resin copper plate". Because the hardness of the disk surface material is between polyurethane and tin, it is also called a way of hard throwing. Using resin copper plate for polishing, and then with special diamond polishing liquid and spraying rate per second, the cutting rate can reach 2.3~2.8um/min. Combined with Grinding's grinding process, a large amount of production output can be increased. Of course, the consumption of diamond polishing liquid will also increase, but under the production mode with lower production capacity and lower risk of loss, the production cost of each chip may not necessarily increase.
4. Discuss the combination of high cutting rate of resin copper disc
The first element is the gap between the copper plate groove and the groove. The width of the gap between the groove and the groove is preferably 1.3 to 1.5 times the width of the groove. Then there is the amount of polishing liquid sprayed, which must be properly set and adjusted according to the clean room environment and the cooling temperature of the copper plate.
Most of the diamond polishing fluids use polycrystalline diamond particles, which are not only stable in cutting, but also have a good cutting rate if the formula ratio with other solvents is good.
Chengdu JiuZhan Technology Co., Ltd.
地址 : No. 1 attached to building 8, No. 1111, Changshengqiao Road, north area of modern industrial port, Pidu District, Chengdu, Sichuan
电话 : 028-61410519
邮箱 : pd@pardang.com
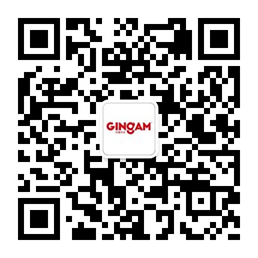
扫一扫 更精彩
Copyright 2022 Chengdu JiuZhan Technology Co., Ltd. all rights reserved. All Rights Reserved 网站建设:聚诚在线